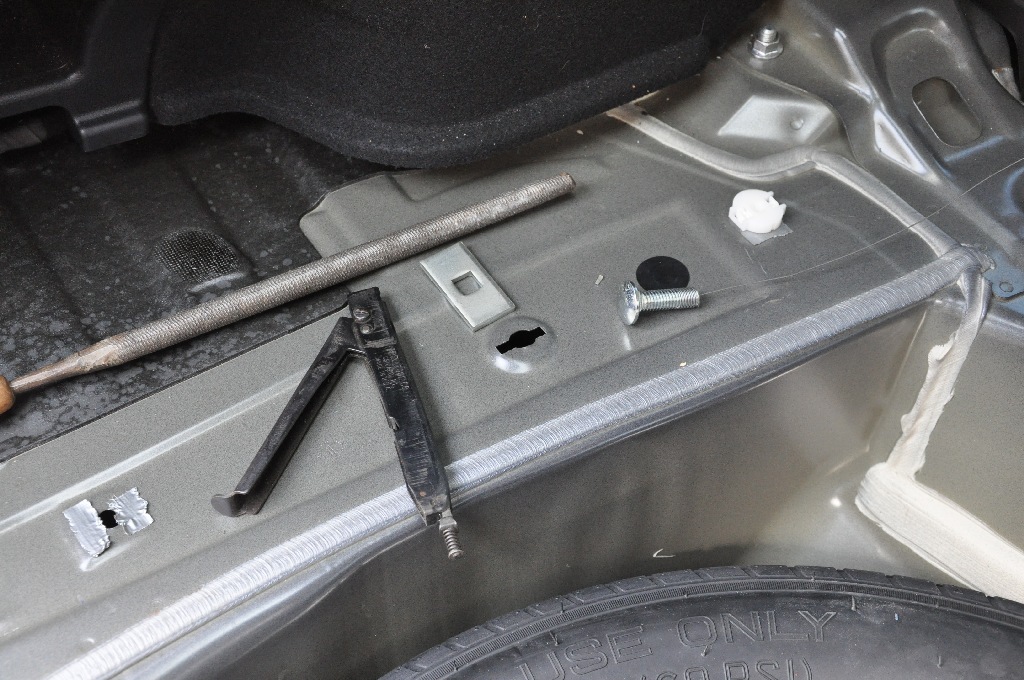
Tools
to make the access hole - a nibbler and round file. Notice the
square edge "wings" on the hole. That's what the nibbler does. To
get access to these holes, you have to unclip 2 difficult foam clips on
each side. See the narrative.
|
I tried making a half-moon instead of a full circle hole. Worked fine.
|
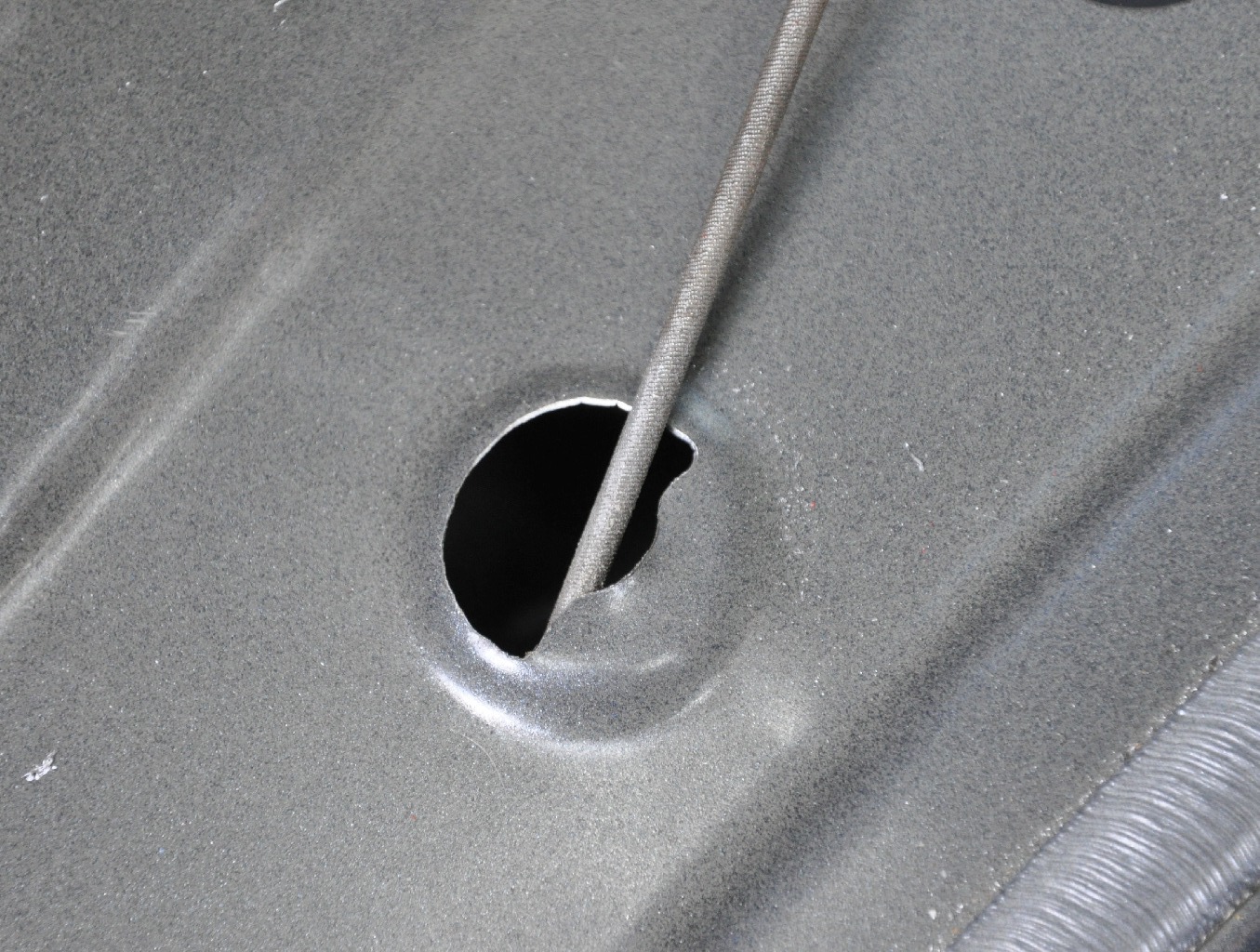
After
using the nibbler and large round file, I finished the hole with a
chain saw sharpening file to get nice smooth edge top and bottom.
|
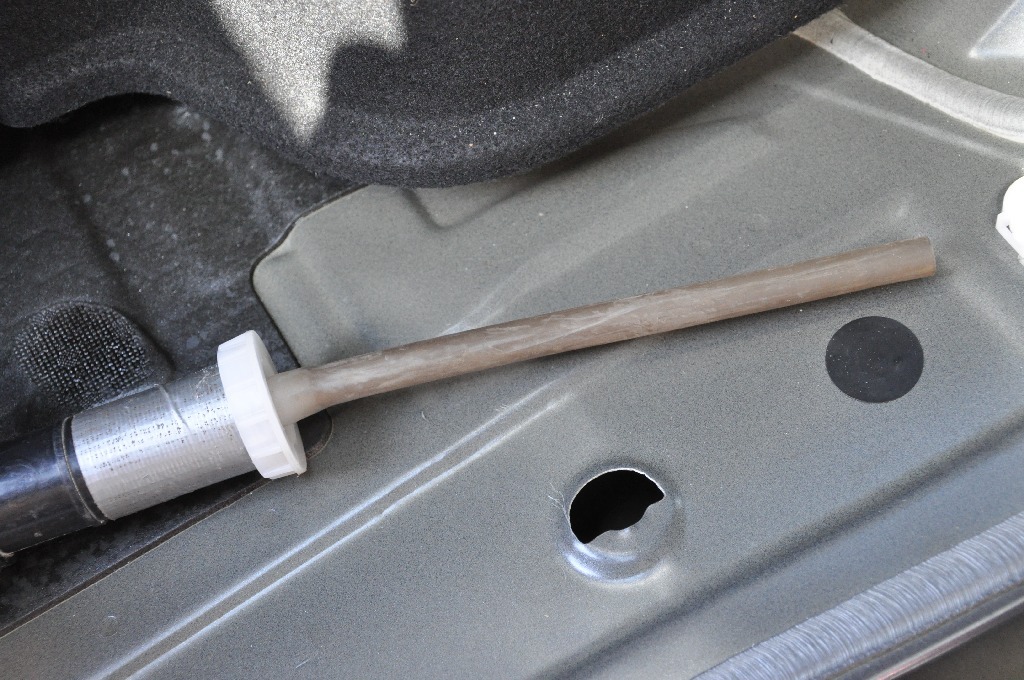
I vacuumed all the metal pieces from inside the hole where the bolts will clamp down.
|
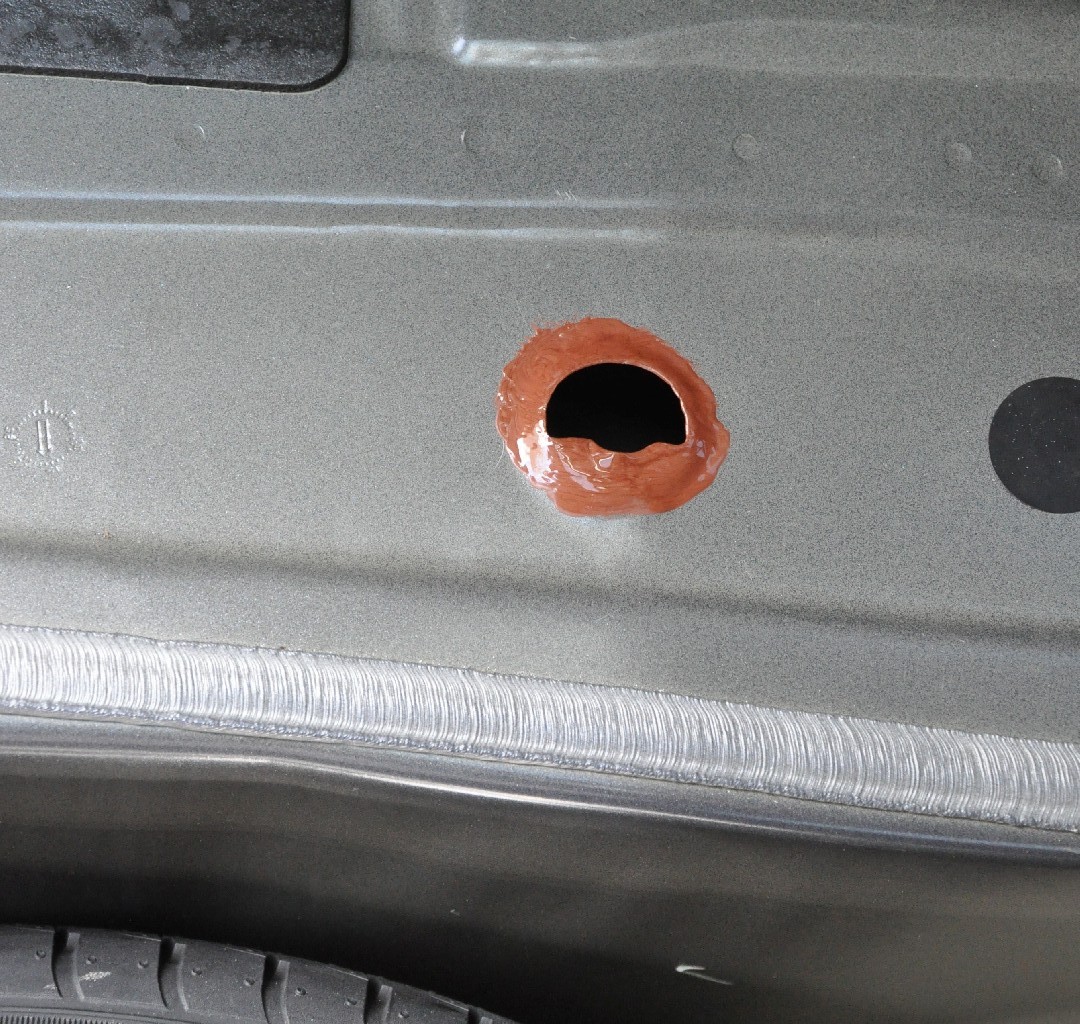
Painted inside and outside of hole with some heavy rust preventive paint.
|
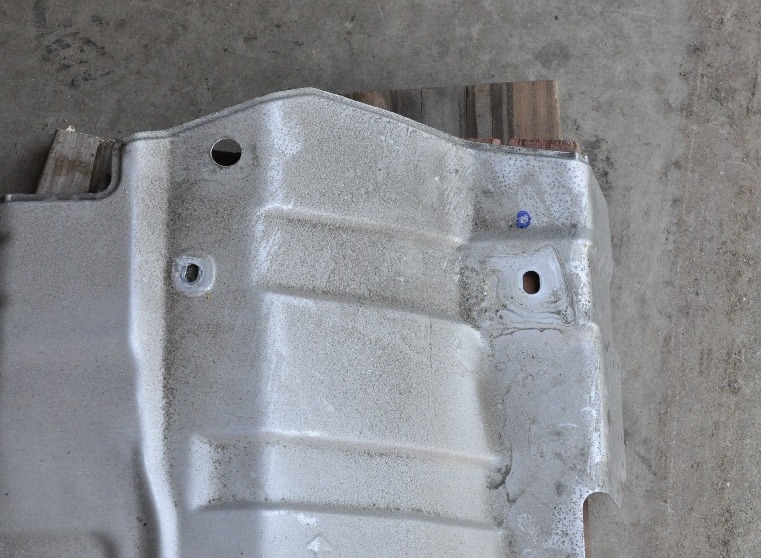
Looking
down the enlarged top holes, the holes in the bottom of the frame box were
visible. Below them, the muffler shield was visible. I
stuck a sharpie down the hole and marked the little blue circle to indicate
where the hitch bolt will be.
|

This is how the left side muffer shield will fit on under the hitch installation. Hitch mounts to frame first, then the heat shield moslty covers the new hitch.
|
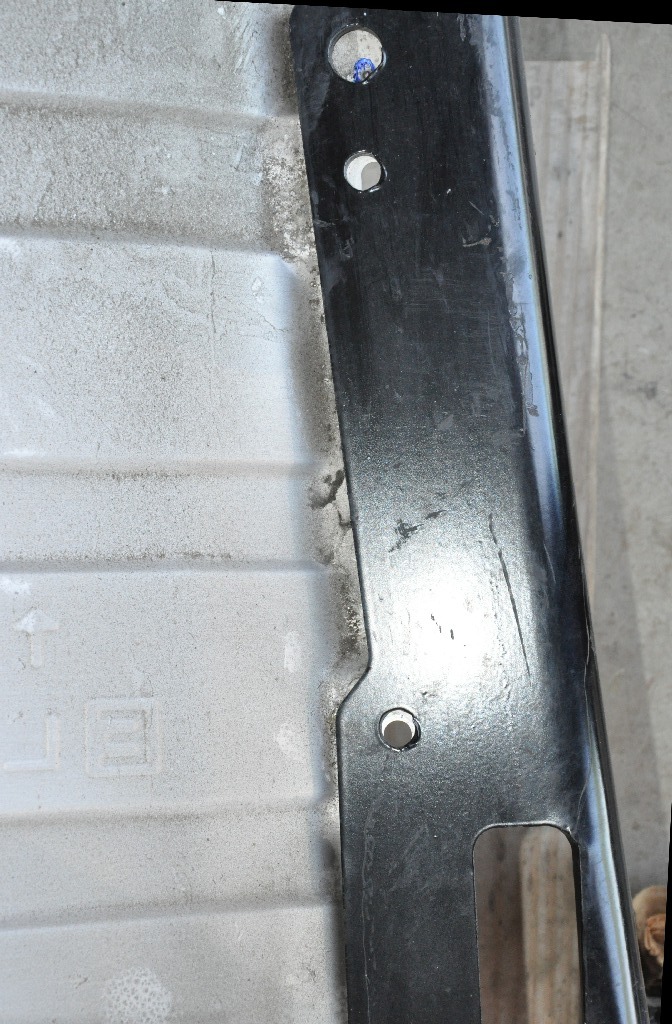
Look
carefuly. The heat shield holes must line up with the little holes of the hitch or the shield screws won't fit back into the car
frame threaded nuts. Check this AGAIN when the hitch is hanging and before its
tightened. I had to really pressure mine into position.
When snug, I checked that the shield bolts fit loosely through the
holes with no binding. THEN I tightened the hitch bolts.
|
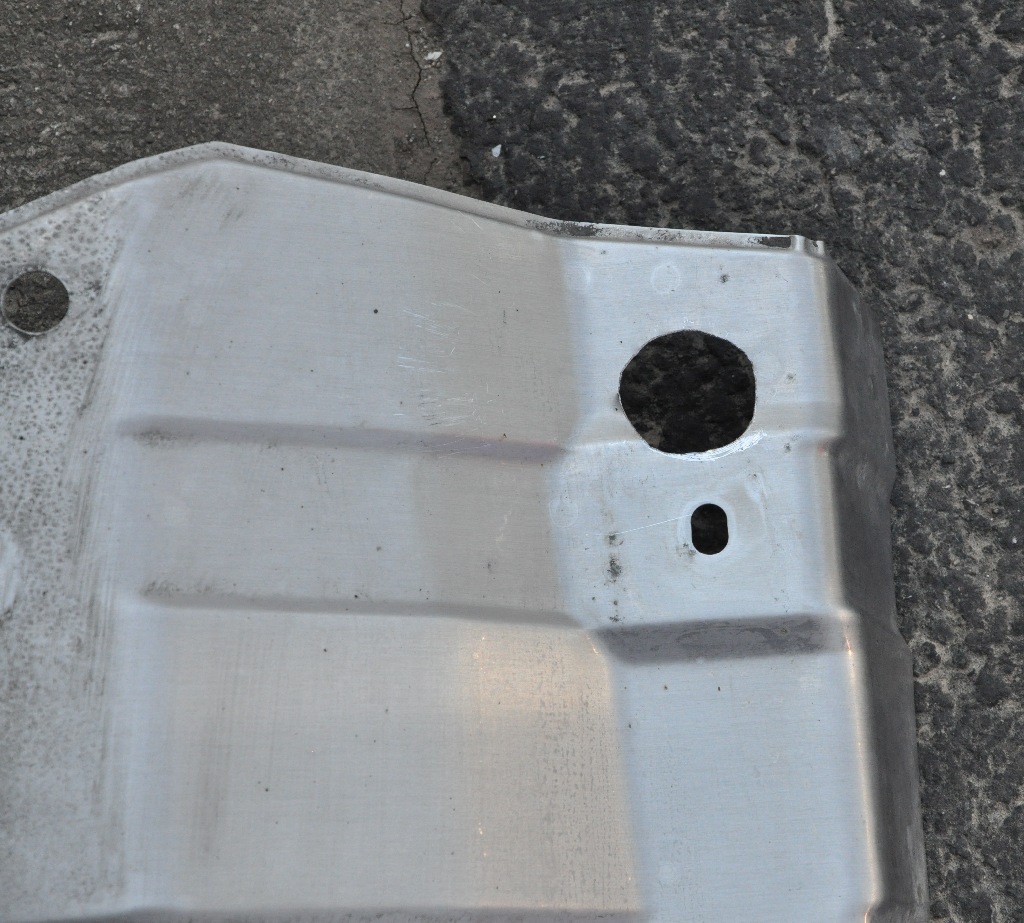
Instead
of hacking off the forward inner corner, I nibbled and filed a nice
roundish hole big enough to fit around the hitch mount nuts and washers.
|
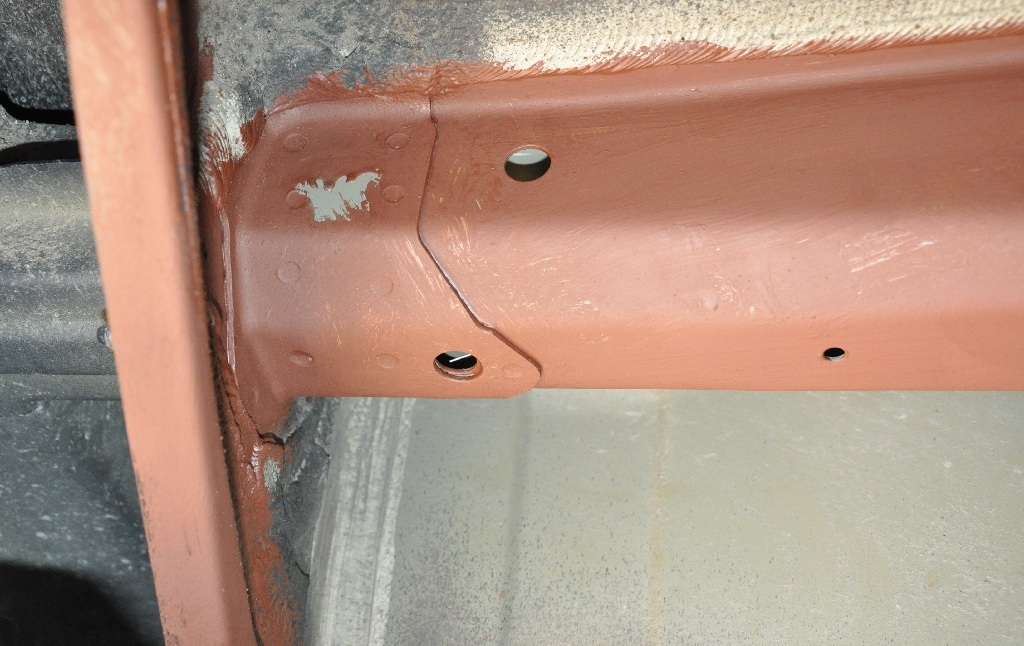
The red color is rust preventative
paint I added. After drying, I fished the bolts through. Look
carefully and you'll see the wire coming from the interior-forward hole
to the after-under hole. There was easy 6-12" extra to poke out the hole. It was no problem to grab with a needle
nose plier and pull the wire out.
|
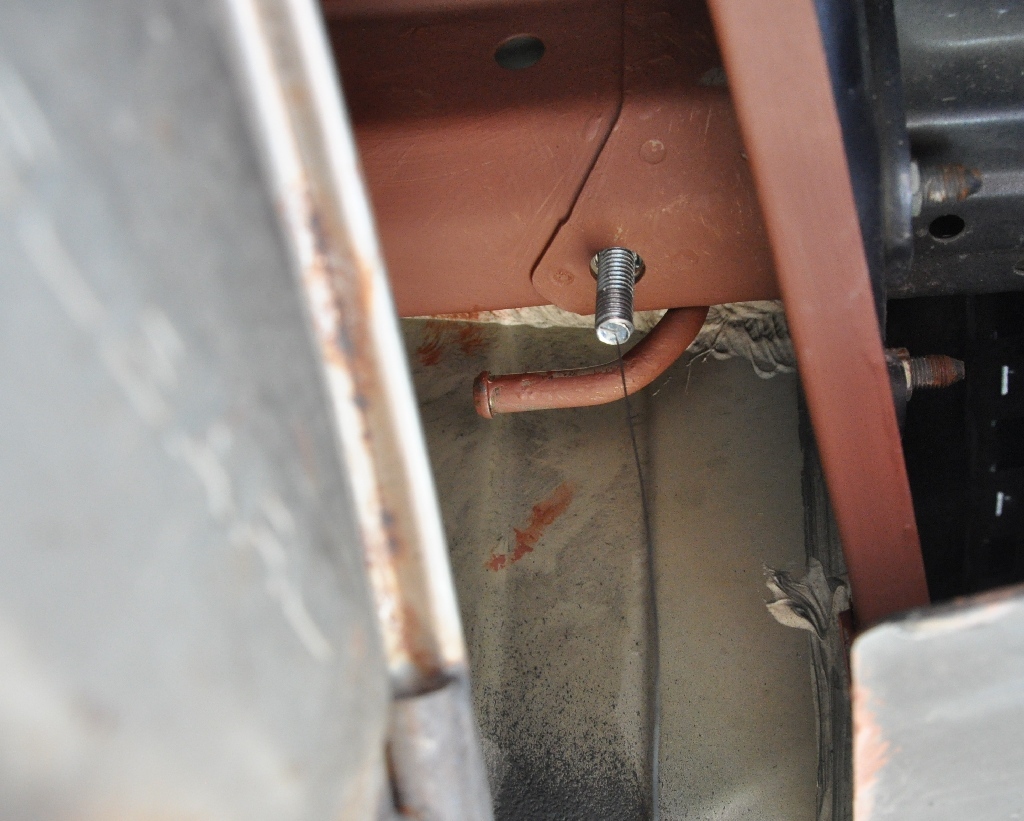
This
is the bolt sticking out the aft mount hole on the left side. The
muffer hangar is visible, too. In a later picture, you can see
how tight the fit is after the hitch is mounted. |
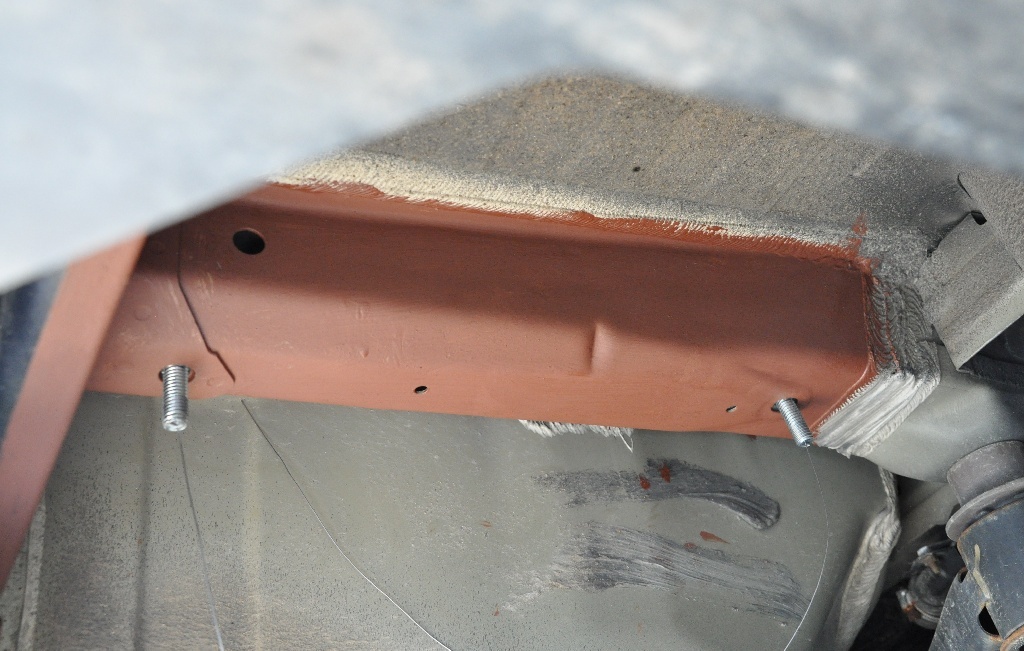
On the right side of the
car, there is lots of room! Once all the bolts and fishwires are
sticking out, you need another person to help lift the hitch into
position withOUT pushing the bolts back, then with one hand unscrew the
fish wire, put on a washer and nut. On the front two bolts, you
also need to insert a spacer washer between the car and the
hitch. (Or preposition it there with tape.)
|
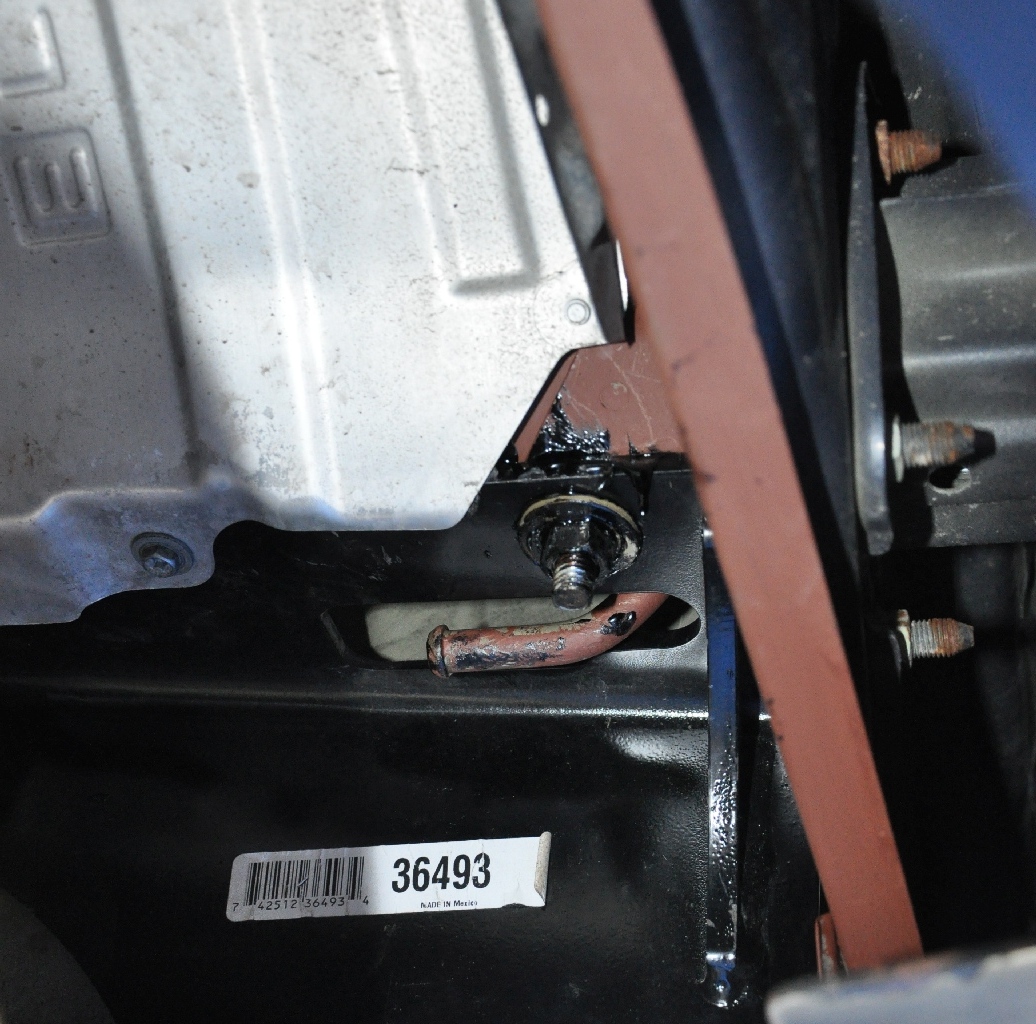
The aft muffler hangar becomes a very tight fit after installing the hitch.
|
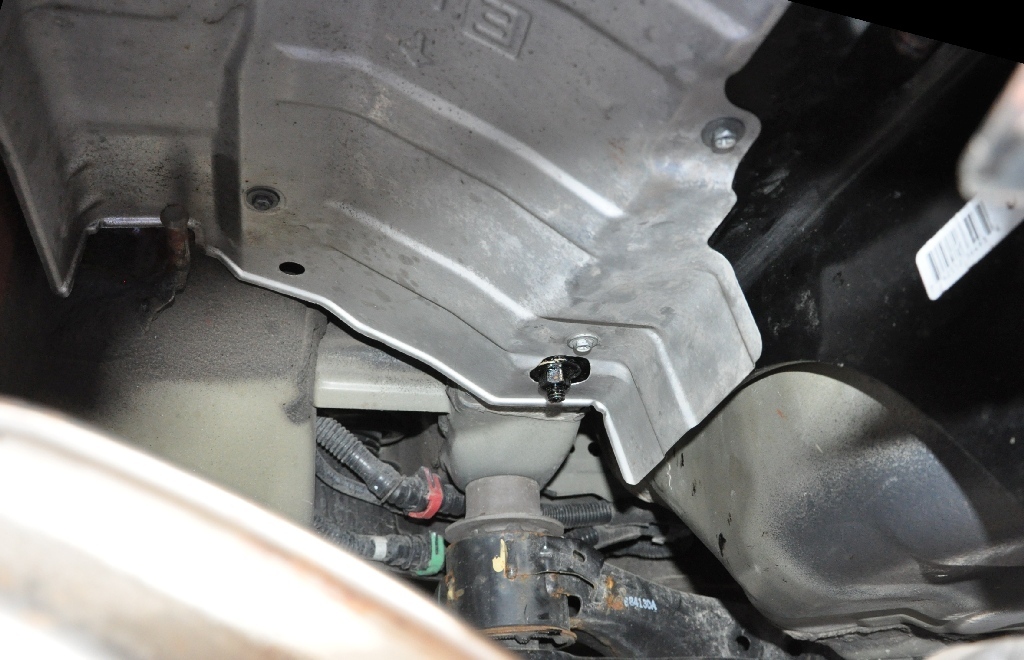
This is how the muffler
shield goes back into position, showing the circle hole around the
hitch bolt. BEFORE you tighten the hitch bolts, without the heat
shield in place yet, make shure the two inner heat shield bolts fit easily through the hitch pre-made holes.
|
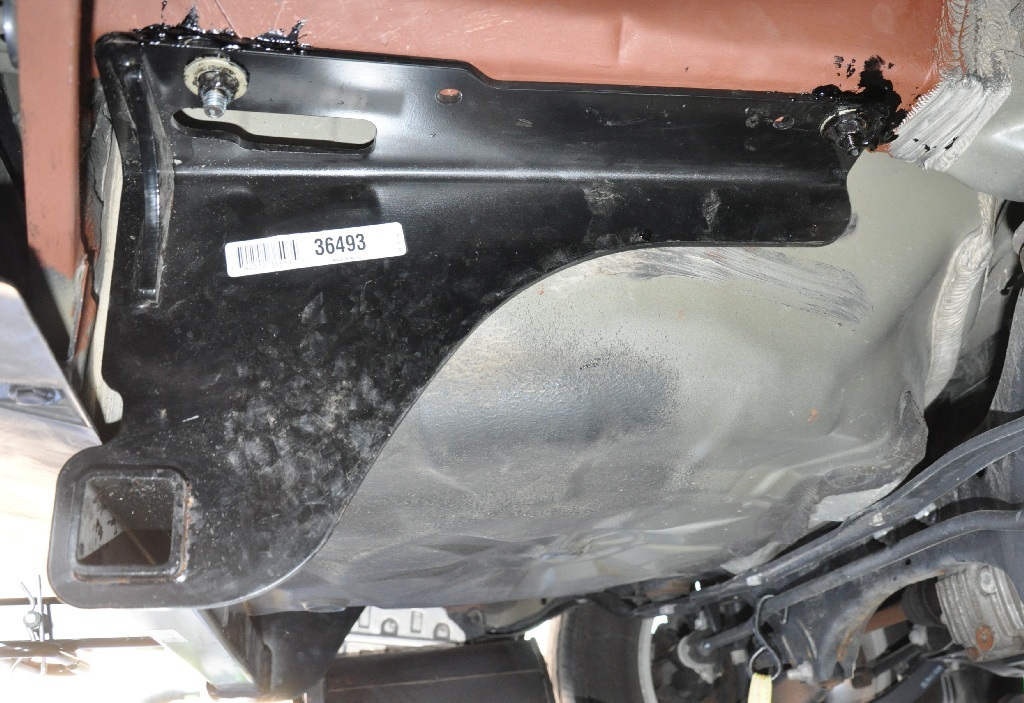
Right side installation. Having good longevity from a
previous hitch installation, I again smeared the bolt joints with thick
asphalt fence paint. I think no water will get in and rust. |
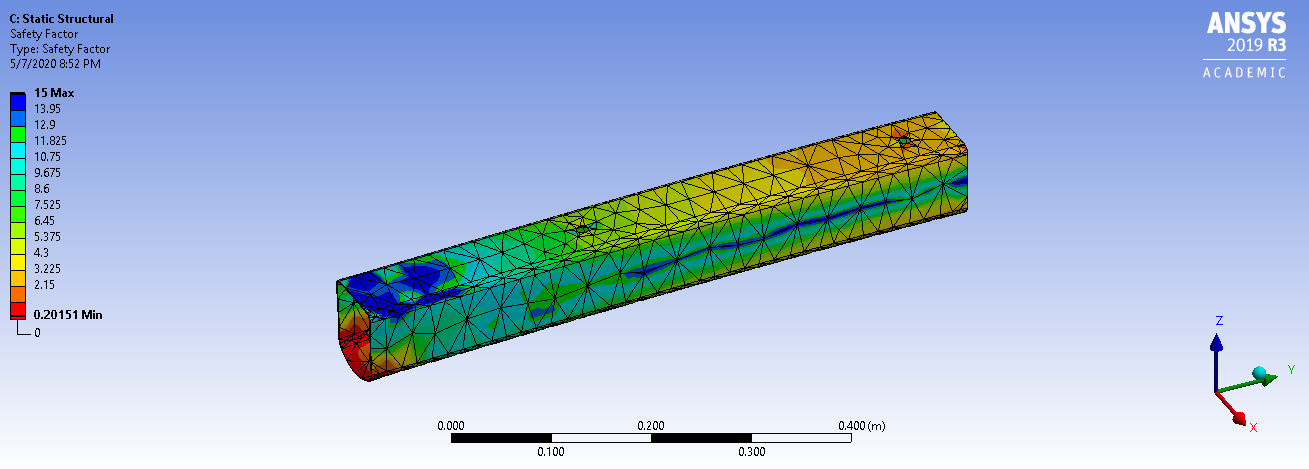
FEA analysis of aft
trailer weight on frame box before drilling the access hole. This is a
qualitative analysis of a heavy weight on a thicker wall box frame.
|
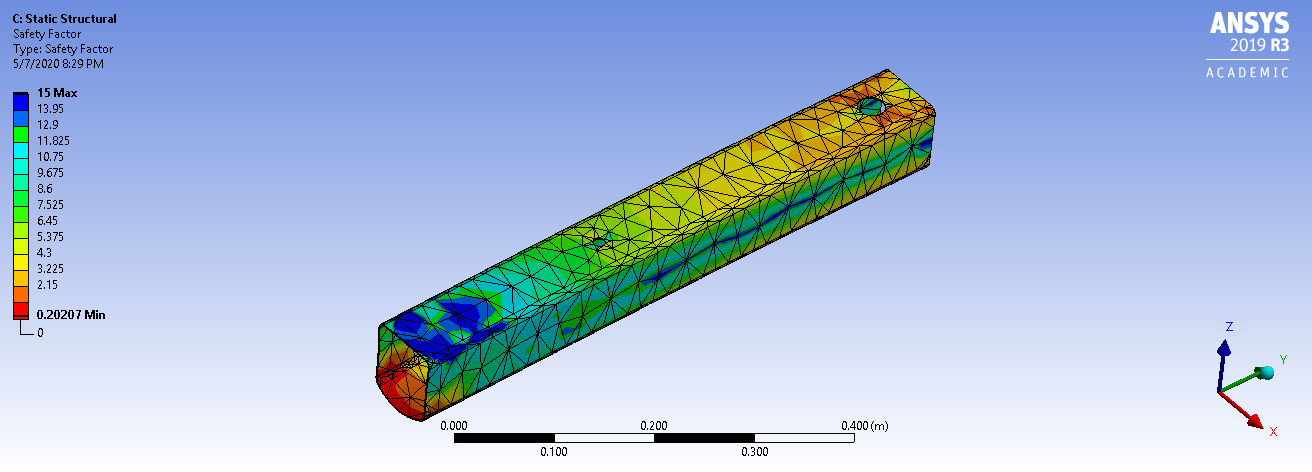
Enlarge the existing top
forward bolt holes to 1-1/8" access (like I did for this project) seems
to cause more stress around the already stressed front hole (more yellow and red color).
|
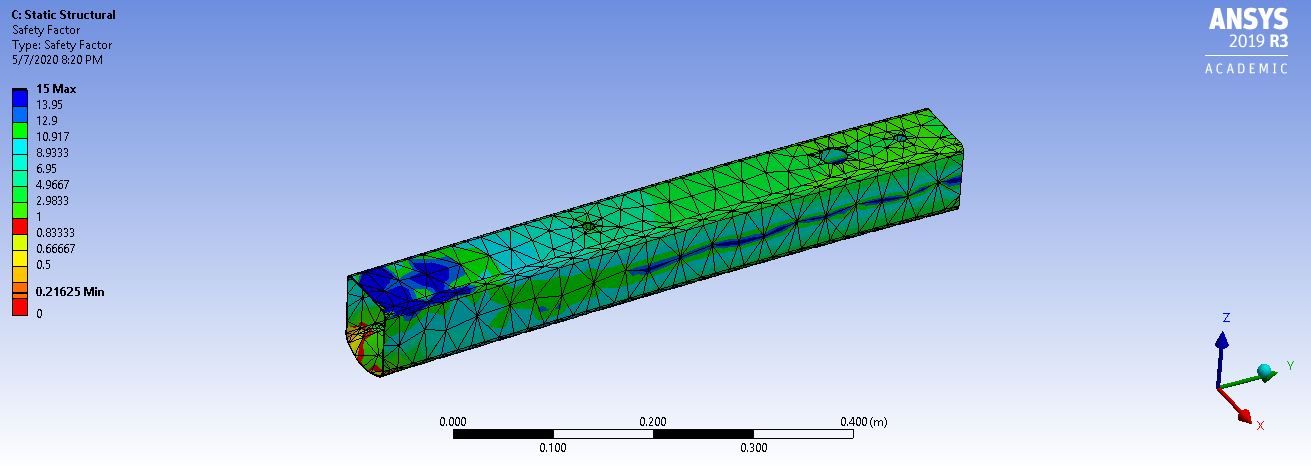
Drill
a new top 1-1/8" hole for access between the holes. Drilling
another hole would have left more safety margin (less yellow and red)! Uh, yea.. this
is what the instructions said but I thought I would be smarter.
Uh.. nope.
|